Project Description
Electronique card – Thermal analysis
This electronic card is composed in particular of a processor, dissipates a considerable thermal energy. To get a good operation and preserve its life time, its temperature should be maintained at a level below a critical temperature. A heat sink and fan are used for this purpose. The study presented here proposes to determine the maximum temperature reached by the processor using the numerical simulation tool in fluid and thermal mechanics.(CFD Computational Fluid Dynamics).
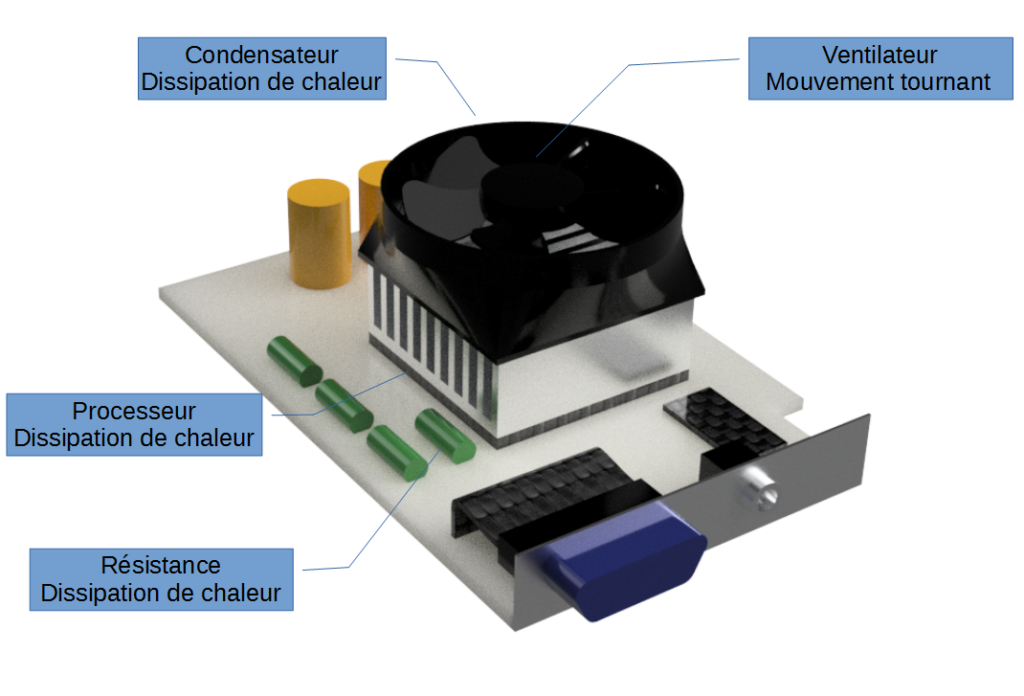
Boundary conditions and physical models
- A thermal power (power density in W / m3) is imposed on the relevant components: the processor, a resistor and a capacitor.
- The movement of the fan is taken into account by imposing a rotational speed.
- The electronic board is located in ambient air at 20 ° C
- The exchange between the air and the dissipator is done mainly by forced convection. Air expansion and natural convection effects are also taken into account in the CFD model.
- A thermal contact resistance is imposed between the processor and the heat sink which can be minimized in practice by the use of a thermal paste.
Résultats
The aluminum heat sink has a relatively homogeneous temperature at any point. Its fins are well fed by the air flow forced by the fan. The dissipation is thus made homogeneously on the surface of contact with the processor. The processor thus reaches its maximum temperature at its center.

![Temperatures [°C] on the dissipating components](https://numairo.fr/wp-content/uploads/2017/01/P03_carte-electronique_t-w-cfd.png)
![Temperatures [°C] of the processor. view from the bottom](https://numairo.fr/wp-content/uploads/2017/03/P03_carte-electronique_t-wproc-cfd.png)
Continuation of the study
Operating and cooling conditions lead to slightly elevated temperatures (81 ° C). It is possible to optimize the heatsink and fan. The power dissipated in the processor is important regarding its low volume which may need the use of another cooling technology with, for example, Peltier modules.
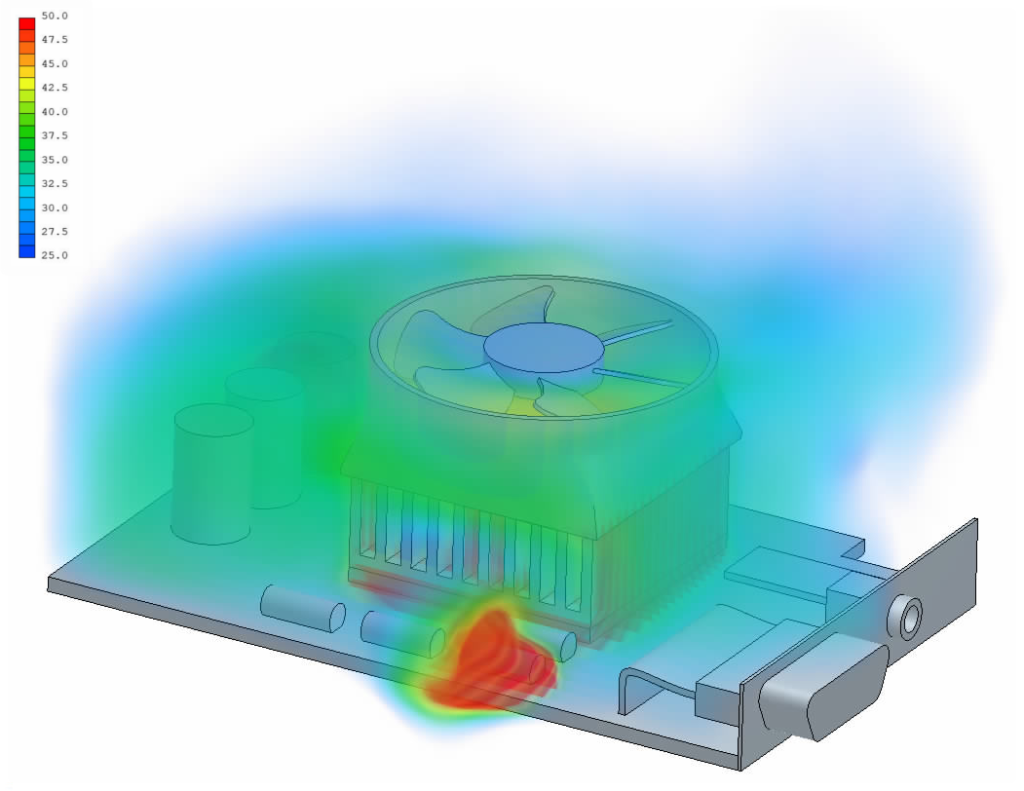
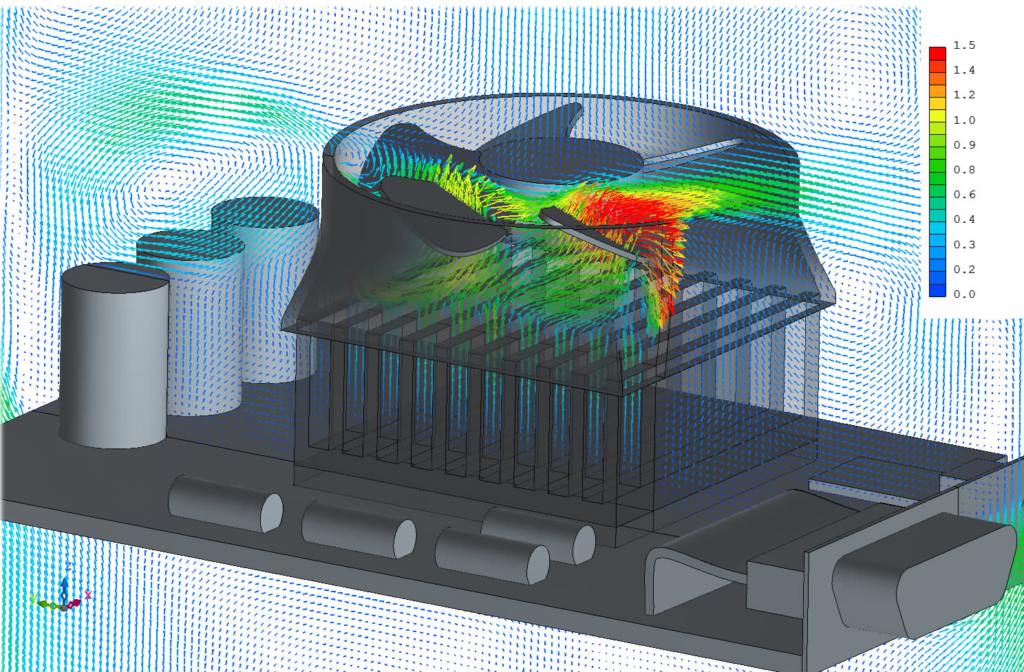