Project Description
CFD analysis for the characterization of a fan
The choice and dimensioning of a fan is based on the knowledge of its flow-pressure characteristic curve. This characteristic is established by measurements (test bench) or numerical simulation in (CFD Computational Fluid Dynamics) considering the apparatus operating at a given speed of rotation. There is indeed a “nominal” rotation speed for which the performances are optimal. It is proposed to make this characterization on the fan model illustrated here, a particular case of the type of apparatus allowing the transfer of mechanical energy with a fluid called fluid machines or turbomachines.https://numairo.fr/wp-admin/post.php?post=1863&action=edit#
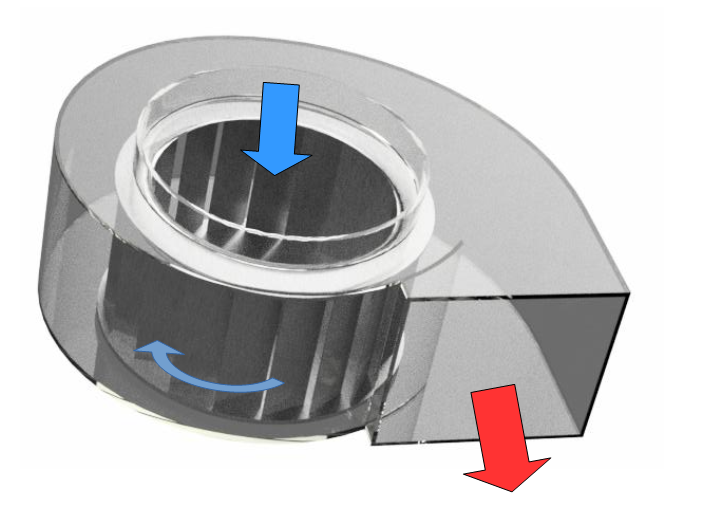
Boundary conditions and physical models
- A flow is imposed as input
- A pressure condition is imposed at the output
- The rotation of the rotor of the fan blades is taken into account
- Turbulence is modeled
Simulation results
Simulation of several operating points (flow-pressure) makes it possible to construct the characteristic curve of the fan. The simulation also gives the possibility to analyze behaviors that could reduce the performance of the device as part of an optimization. Other information that may be important for some applications where homogeneity of speed is important is that the velocity profile at the output of the apparatus is very unbalanced towards the outside of the volute.
![Velocities in the median plan of the fan [m/s]](https://numairo.fr/wp-content/uploads/2017/01/P08_ventilateur_vitesse-cfd-1024x655.png)
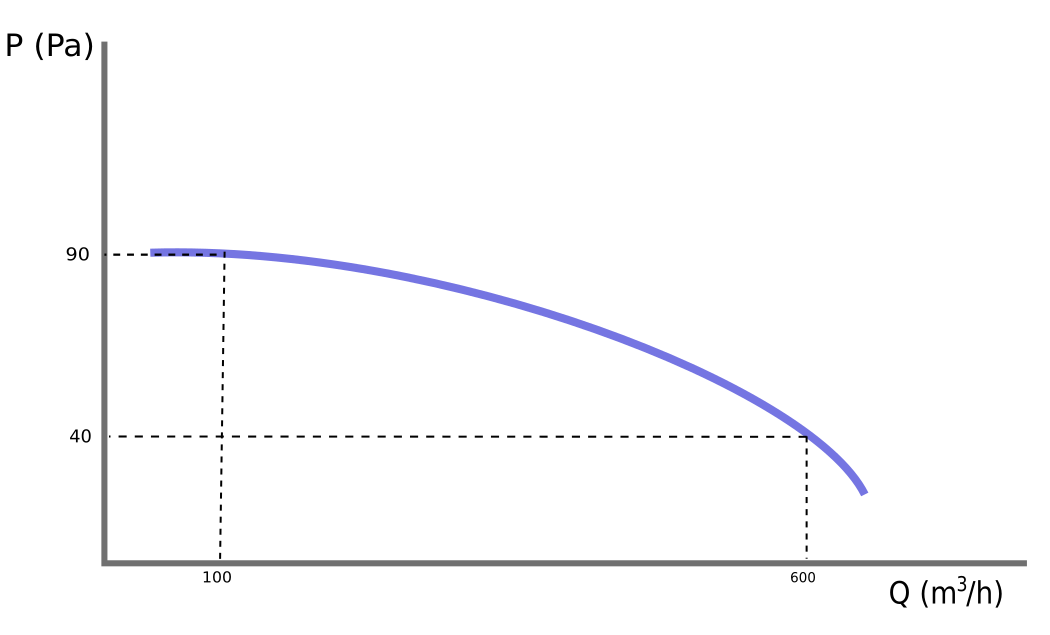
![Total pressure [Pa] on the inlet and outlet of the fan](https://numairo.fr/wp-content/uploads/2017/01/P08_ventilateur_pression-totale-cfd-1024x687.png)
Computational Fluid Dynamics (CFD) can be useful for working on the structure of the fan. In fact, during operation, the fan and in particular the rotor is subjected to pressures which may vary over time. These pressures may be due to:
- to the reaction forces of the thrust of the fan on the fluid
- to an aeraulic vibratory phenomenon due to vortex releases or to an interaction between the moving and static parts of the turbomachine.
Variable stresses on materials may cause fatigue wear. The CFD Computational Fluid Dynamics simulation allows to detect these vibrations or variable loads. The pressure fields over time can be used to carry out a mechanical calculation of the structures in order to determine the stress levels and conclude over a lifetime.
The frequency of the stress is also determined, which is interesting to compare with the frequencies of the eigenmodes of the structure of the apparatus determined by a modal calculation, in order to avoid any risk of resonance.
![Lignes de courant colorées par leur vitesse [m/s]](https://numairo.fr/wp-content/uploads/2017/01/P08_ventilateur_pathlines-cfd-1024x679.png)
![Pression statique sur le rotor du ventilateur [Pa]](https://numairo.fr/wp-content/uploads/2017/01/P08_ventilateur_pression-statique-cfd-1024x679.png)
![3D renderring of velocities in the fan [m/s]](https://numairo.fr/wp-content/uploads/2017/01/P08_ventilateur_rendu-cfd-1024x678.png)