Project Description
CFD analysis of a cooling of hot smokes by dilution of fresh air
Some industrial processes use hot fumes. The temperature must be controlled to optimize the treatment of these fumes (chemical reactions) and to protect installations which are liable to damage if too high heat reaches them (bag filters). Several solutions are possible to cool the fumes. These include the use of a cooling tower that is presented at this site, or dilution with fresh air.
It is proposed here to study a dilution installation by means of numerical simulation in fluid mechanics and thermal (CFD Computational Fluid Dynamics). The size of these installations must take into account the pressure level in order to ensure a vacuum in the fresh air intake area so that the smoke does not escape, but also the mixture of the air collected with the fumes. Indeed, the flows of hot fumes which can be formed as a result of the capture of air can also create damage on a part of the downstream apparatus to be protected.
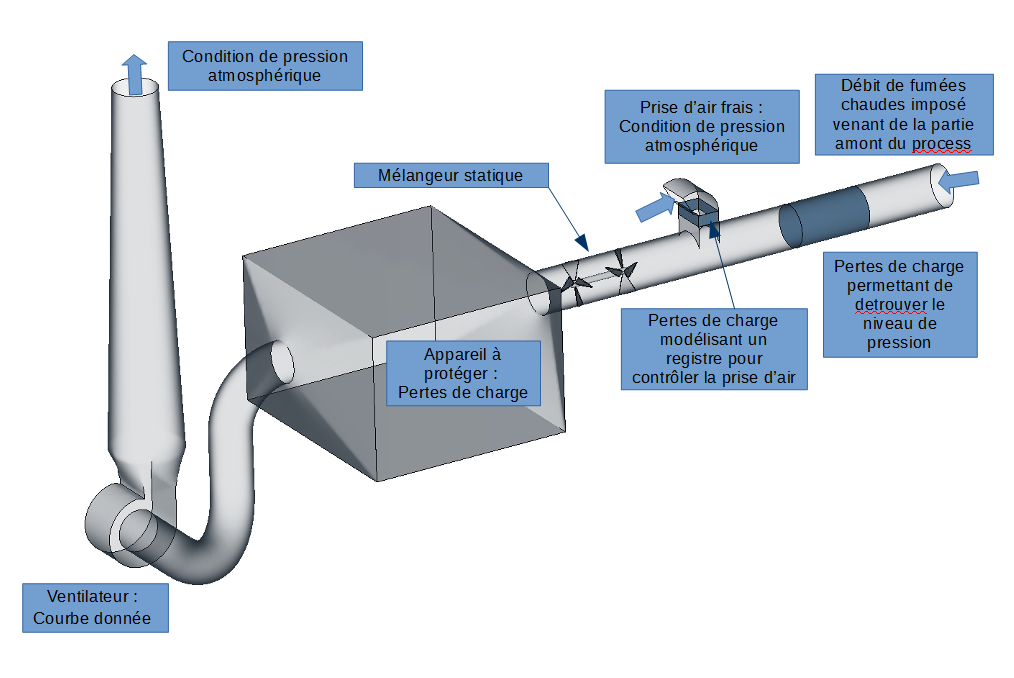
Boundary conditions and physical models
- A flow of hot fumes from the upstream process is given
- A pressure drop is imposed, making it possible to fix the pressure level which will be the engine of the fresh air intake
- A fan, modeled by its characteristic curve, makes it possible to circulate the fluid
- The apparatus to be protected is taken into account by a homogeneous medium imposing equivalent pressure drops
- An atmospheric pressure is imposed at the chimney outlet.
- An atmospheric pressure is imposed at the level of the dilution tapping
- A pressure loss at the dilution tapping model models a register to control the flow of fresh air.
Simulation results
![Pressures [Pa] on the walls of the device](https://numairo.fr/wp-content/uploads/2017/01/P14_dilution_pression-parois-cfd-1024x626.png)
![Temperatures [°C] on the walls of the device](https://numairo.fr/wp-content/uploads/2017/01/P14_dilution_temperatures-parois-cfd-1024x643.png)
![Velocities [m/s] in the median plane of the device](https://numairo.fr/wp-content/uploads/2017/01/P14_dilution_vitesses-plan-cfd-1024x600.png)
![Mass fraction of smokes [Kgsmokes/Kgmix] in the median plane](https://numairo.fr/wp-content/uploads/2017/01/P14_dilution_fumee-plan-cfd-1024x608.png)
The static pressure levels on the walls of the installation are balanced with the stress which is the vacuum of the fan and the flow rate imposed at the inlet of the hot flue gas from the upstream of the process, with the pressure drops of the various elements on the line. From the inlet of the fumes to the fan, the line is depressed, allowing the line to be opened to the atmosphere in order to place the dilution sluice and which ensures that the smoke does not escape.
It is possible to estimate the flow of incoming air, in this case one quarter of the flue gas flow. The visualization of the air temperature and presence profiles in the flow shows that the fresh aspirated air does not mix naturally with the fumes but that these two gases continue to travel in the ducts in a very independent manner (blue zone and red on the boards concerned). The presence of the static mixer, consisting of blades that induce the fluid to take a rotational movement, then the same blades, but urging the flow to straighten, is essential to break this separation between the two gases (smoke and air).
The space available for mixing is restricted, however, it would be possible to attempt to separate the two batches of blades and to work on their inclination in order to optimize the mixing.
![Pressures [Pa] applied on the walls of the static mixer](https://numairo.fr/wp-content/uploads/2017/01/P14_dilution_pression-melangeur-statique-cfd.png)
The pressure field on the blades is plotted to show that the structural aspect of this element can be taken into account for its dimensioning by introducing this pressure field as loading condition for a FEA Finite Element Analysis, or by extracting macroscopic quantities such as the reaction forces of the fluid on these blades.
![Pathlines colored by their velocity [m/s]](https://numairo.fr/wp-content/uploads/2017/01/P14_dilution_lignes-courant-vitesse-cfd-1024x645.png)
![Pathlines colored by their velocity [m/s] - focus on the static mixer](https://numairo.fr/wp-content/uploads/2017/01/P14_dilution_lignes-de-courant-vitesse-cfd-1024x679.png)