Project Description
Adjusting the smoke extraction rate by a suction hood – Thermo-mechanical analysis
The iron and steel industry is an industrial sector affected by smoke emission, particularly in work environments. Occupational hygiene standards recommend exposure thresholds for the pollutants present in these smokes. This imposes to collect at the emissions source on each station that release smoke.
We propose here to study to collection of one of these posts. A steel ladle releases hot smokes. A hood with its suction flow is dimensioned. Numerical simulation in fluid mechanics and thermal exhanges (CFD Computational Fluid Dynamics </ span> ) test the proposed configuration by checking the quality of the capture. Capture efficiency, defined as the proportion of smoke captured in relation to the amount of smoke released, is an objective quantitative criterion that can be evaluated using the numerical simulation tool.
In addition, as part of the design assistance for the hood, the temperatures on the hood can be used to evaluate the thermomechanical stresses (FEA Finite Element Analysis) due to the temperatures spacial changes on the installation caused by the radiation of the free surface of liquid steel at very high temperature.
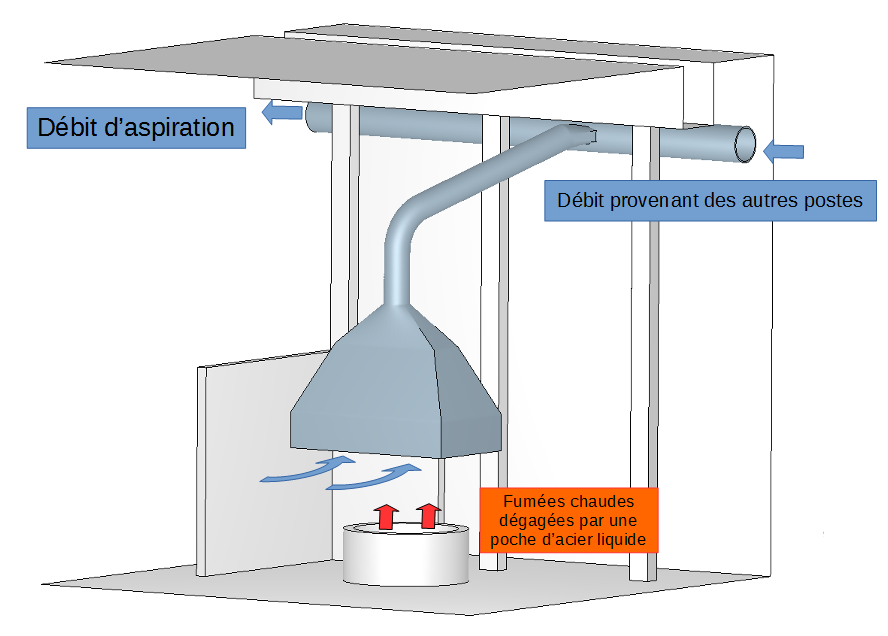
Boundary conditions and physical models
- A suction flow is set at the extremity of the duct
- Ambiant pressure and temperature is set on the opened area on the hall
- A hot smoke flow from the ladle is given.
- A surface temperature is given on the free surface of the liquid steel and on the ladle walls
- The thermal expansion of air and smokes and gravity lead to bouyancy.
- The goal of the study is to analyse the smokes collection and the temperature field on the hood as well. In consequence, radiation heat transfer is taken into account.
- Heat conduction is modelized in the thickness of the hood.
Simulation postprocessing
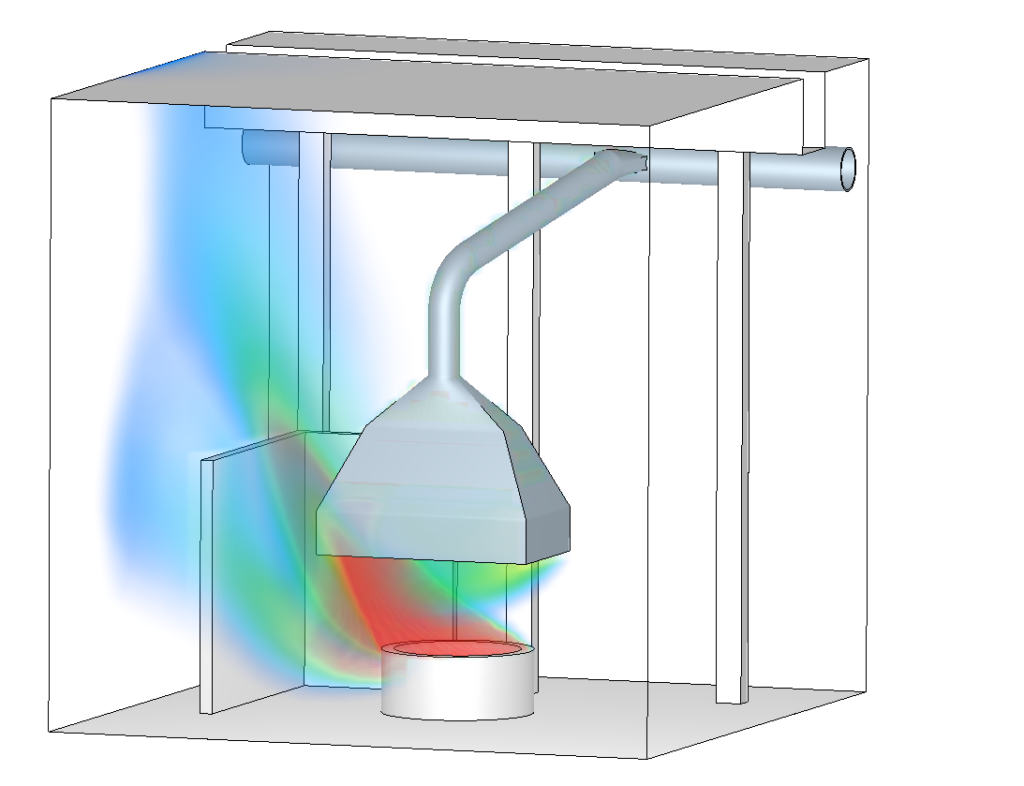
The two above pictures compare the smoke collection for two suction flows (ratio of 1 to 3). The gain of collection efficacity between the two above configurations is visible. However, if the operator’s objective is to approach “zero emissions”, increasing the flow will not be the best solution. It will be proposed to work the design of the hood towards more confinement.
Moreover, the pressure field shows that a considerable pressure loss occurs in the throttle at the top of the hood and all along the small diameter duct, which increases the power required at the same suction flow rate.
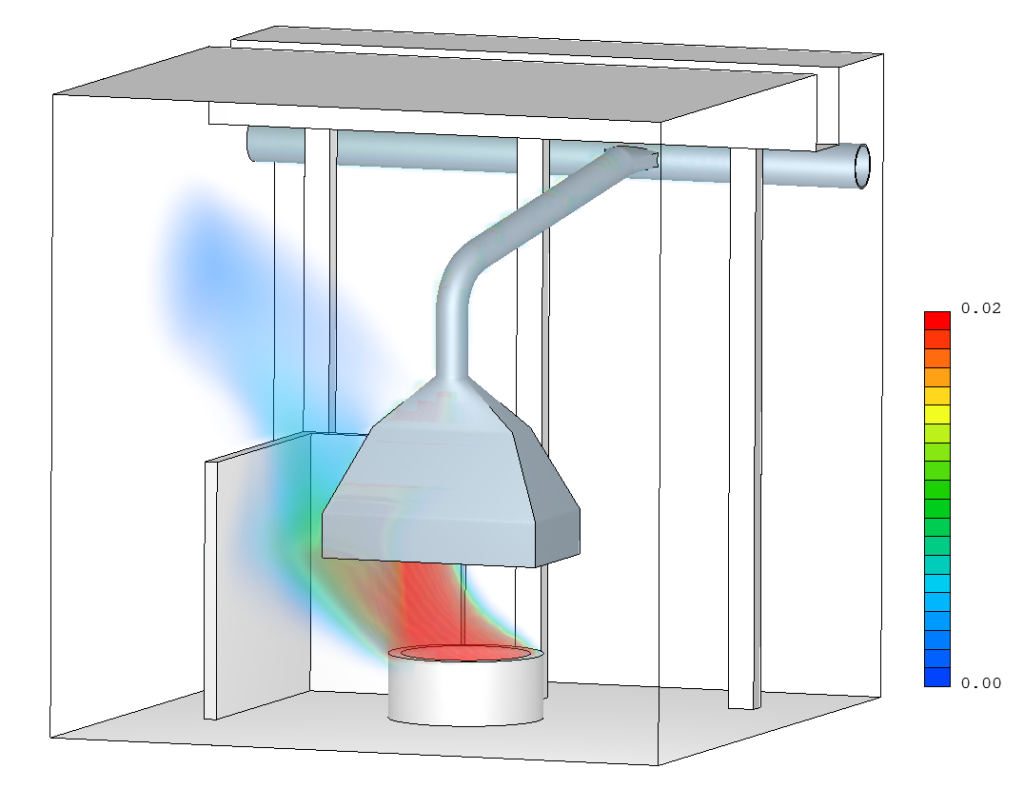
![Pressure [Pa] on the internal walls of the hood](https://numairo.fr/wp-content/uploads/2017/01/P13_hotte-aspiration_pression-hotte-cfd-1024x779.png)
![Streamlines colored by velocity [m/s]](https://numairo.fr/wp-content/uploads/2017/01/P13_hotte-aspiration_streamlines-vitesse-cfd-1024x765.png)
Thermal and thermomechanical behaviour
![Temperatures [°C] on the wall around the ladle](https://numairo.fr/wp-content/uploads/2017/01/P13_hotte-aspiration_temperature-cfd-1024x834.png)
![Temperatures [°C] on the walls of the hood](https://numairo.fr/wp-content/uploads/2017/01/P13_hotte-aspiration-cfd-temperature.png)
![Temperatures [°C] in a plan passing through the ladle and the hood](https://numairo.fr/wp-content/uploads/2017/01/P13_hotte-aspiration_temperature-plan-cfd.png)
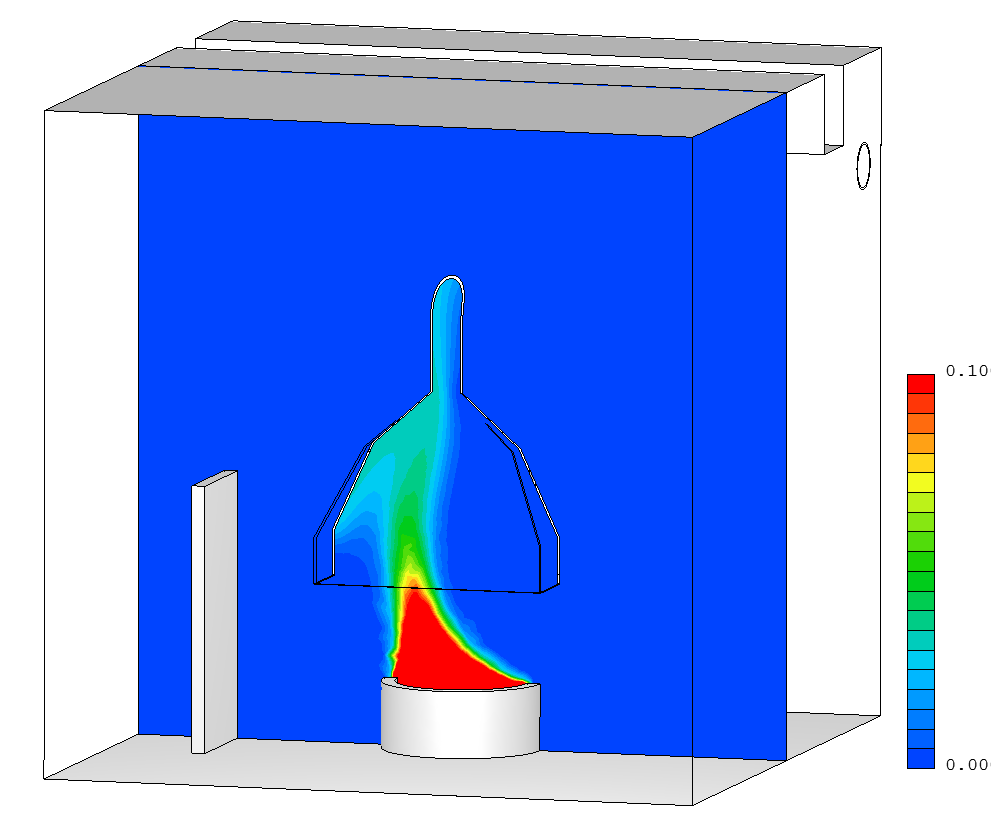
The temperatures measured on the walls around the ladle is high. The hood itself undergoes a significant rise in temperature. The visualization of the temperature of the smokes shows that they are already diluted with air and cooled when they touch the hood. The high temperature of the hood is thus explained by the intensity of the thermal radiation received from the liquid steel (1500°C). The hood itself radiates energy to the surrounding walls.
This high temperature of the hood is not homogeneous. There is a rapid variation in temperature as when we move away from the steel ladle. The thermal gradient is particularly important in the convergent round-square transition at the top of the hood. This temperature variation suggests the occurrence of thermomechanical stresses. This is shown on the picture below showing the results of a static linear study in structural mechanics (FEA Finite Element Analysis) from the temperature profile in the fluid and thermal mechanics calculation (CFD Computational Fluid Dynamics). The stresses observed are far above the elastic limit of the steel at these temperatures.
![Magnitudes of displacements on the hood [m]](https://numairo.fr/wp-content/uploads/2017/01/P13_hotte-aspiration_deplacement-fem-cfd-1024x781.png)
![Von Mises stresses on the hood [Pa]](https://numairo.fr/wp-content/uploads/2017/01/P13_hotte-aspiration_contraintes-vonmises-fem-cfd-1024x812.png)